Maximizing Container Efficiency in Logistics
Mitigate Container Unavailability and Realize Cost Savings
Containerization — a system of specialized intermodal container assets to transport ingredients, raw materials, parts, and finished products from one place to another — has been one of the most revolutionary changes to impact supply chain logistics.
Before the 1950s, product was exposed, creating potential damage and theft. Materials were loaded onto vessels in oddly configured structures requiring organizational skills to best organize and utilize the vessel space. Today, containerization is the predominant form of “unitizing” transport goods. It uses ground, rail, and sea vessel transport (Figures 1-3) with purpose-built equipment to optimize the modern container [1].
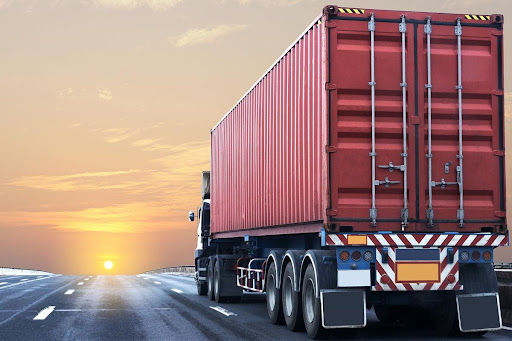
Figure 1.
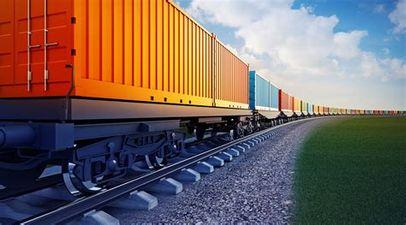
Figure 2. Rail Transit
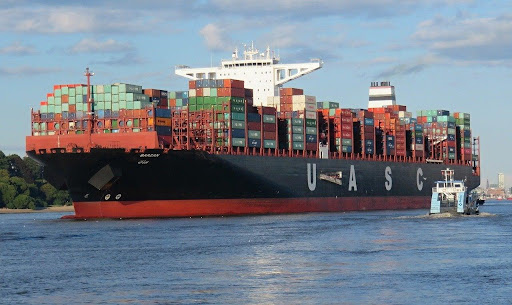
Figure 3. Sea Transit
There are five primary container sizes (Figure 4), with 90% falling within the 20’ x 40’ range. Ratings, classifications, and dimensions are defined by International Organization for Standardization standard 668:2020 [2]. With these standards in place, focus can be placed on the best use of available space and load capacity within each container. This is especially important with recent global shortages.
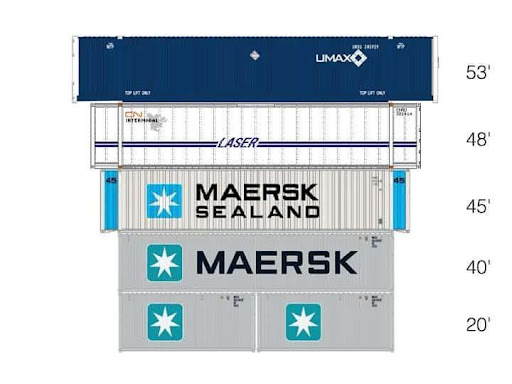
Figure 4. Size Comparison[3]
Addressing container availability problems and rising cost challenges is a top concern for transportation and supply chain managers. A logistics manager at a well-known consumer packaged goods company shared some insight about the effort to manage the current market: “We are looking at every option to try and manage costs; because not only have costs gone up, but supply is difficult to find as well.” Unfortunately, this is an all-too-common perspective.
So, what lever can a supply chain manager pull to begin the mitigation of container availability problems and increasing costs? One option is maximizing volume usage efficiency, which lies completely in the shipper’s control.
Optimal efficiency is achieved when the container both weighs and cubes out. These two attributes rarely intersect to form the perfect load. However, savings opportunities lie in the gap between the current load configuration and a future, more efficient composition.
This approach requires a thorough review of the supply chain transportation network and a full understanding of the current pallet configurations and packaging performance capability.
Maximize Container Efficiency with ALOE Group
At ALOE Group, our team will lead you to more efficient use of containers. We will evaluate the current packaging and pallet configuration profiles and compare the results to multiple predictive alternative structures. This will result in more cases per pallet, leading to more cases per container. Normalizing for volume results in fewer trucks needed in aggregate. A savings calculation is generated based on the reduction of trucks per lane for each stock-keeping unit (SKU) involved.
ALOE Group will also consider, evaluate and verify the packaging implications of changing the cases per layer or per pallet. Our team understands static and dynamic top loads and pallet stability to ensure product integrity during shipment. ALOE Group leverages the package engineering resources of its parent, Stress Engineering Services, to evaluate performance and compare it to current pallet and packaging performance. This work is typically done at your manufacturing location, with supplemental testing performed at the Mason, OH, labs.
Maximizing container efficiency reduces the need for containers in aggregate and is a part of larger cost savings and reduced SKU transactions.
References: